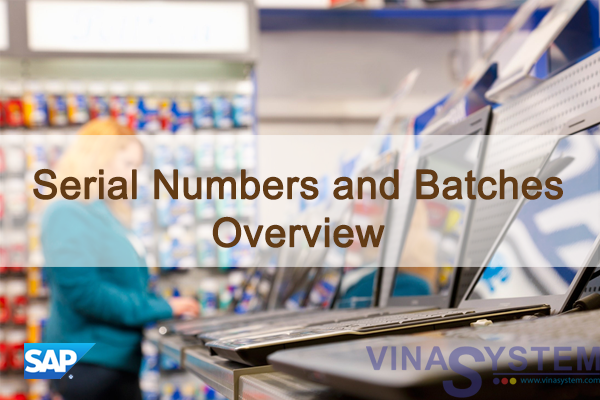
Tài liệu quản lý hàng hóa theo số Serial và lô hàng trong SAP Business One
The topic "Serial Numbers and Batches" in SAP Business One, we will explore two of the methods for tracking items you purchase, make or sell: serial numbers and batches.
We will look at how to create and use a batch-managed items.
We will look at how to create items and use items managed with serial numbers.
I/ Business Scenario
Imagine that:
- Your company would like to more closely track items that they make, buy and sell through their lifecycle.
- Some of the more expensive items, such as laptops and desktop computers, are managed by serial numbers. Each individual laptop or computer has a serial number so that you can easily track sales and service for that particular laptop or computer.
- Others items, such as printer cartridges, are purchased in lots and are managed by batches in order to track expiration dates.
II/ Serial Numbers
Serial numbers can help you track items down to the level of each individual object in your warehouse, so you know exactly which one was sold to a customer.
Serial numbers are also very useful as a way to track service history for a customer’s purchase.
Here are two criteria that can be used to decide if an item should be serialized:
- Is the item a high value item?
- Should the item be tracked for security or repair reasons?
If the answer to both questions is yes, then the item is a good candidate for serial numbers.
II/ Serial Numbers and Batches
In contrast, batches are used to track a quantity of an item with characteristics in common. These characteristics might be attributes you define, such as a shade of color, granularity or PH balance. The characteristics could be dates, such as expiration dates, manufacturing date, or the date the items were received into inventory.
A good example of a batch-managed item would be milk. Each batch of milk has a sell-by date. It is very important to track this date and make sure the milk is sold before its expiration date.
1/ Management Method
You have the option to set the serial numbers or batch numbers to be assigned on every transaction or to be assigned on release only.
This is controlled by the “management method” field on the item master record. The two options are called “on every transaction” and “on release only”.
2/ On Every Transaction
If you choose “on every transaction” then you must assign serial number attributes for every single unit at the first point it enters inventory.
Thereafter, the system will prompt you for a serial number on every transaction where the item is issued out of inventory or returned to inventory.
This way you know exactly which objects are in inventory and which objects have been shipped to a customer.
This method is useful when you need to track the individual objects at all times, and where the receiving personnel have the appropriate information at the time the units are received.
When you first receive the serialized items into stock, you can choose the option to enter serial numbers manually or to create serial numbers automatically using a serial number string of your choice.
3/ Release Only
“On release only” means that serial numbers are only required on documents that issue an item out of a warehouse.
Release documents not only include: goods issue, delivery, A/R invoices and goods issues to production, but also inventory transfers between warehouses and return and credit documents.
When you use “On Release Only” at the time of purchase, there is no need to enter serial number attributes. However, when you remove the item from inventory, the serial numbers for these objects must be created first using the Serial Item Management window.
An alternate option is to choose “automatic serial numbering creation on receipt”. When you purchase the serialized item, the system automatically creates successive numerical serial numbers for the quantity you have purchased. With this option, you can immediately release these objects without further operations. You can update the serial number attributes at a later stage, using the Serial Item Management window. This is especially useful when a large quantity is produced or purchased.
Why might you choose “on release only”?
One example might be if you manufacture an item and would like to issue it into inventory without a serial number. This way, you can wait to assign the serial number until item is picked for delivery. “Release Only” gives you the flexibility to not worry about serial numbers inside the warehouse.
III/ Optional Allocation
Unlike release documents that issue stock from inventory, serial and batch information is always optional on sales orders, because sales orders do not have any effect on inventory, except to create a commitment. If you would like this commitment to capture information about a specific serialized item or specify a batch to be sold, then you can do so in the sales order.
Reserving specific serial numbers or batches at the time of the sales order allows for better control and inventory planning. Perhaps you build some customized computers as special orders for customers. In that case, you may wish to designate a serial number in the sales order that will follow the computer through the customizing process until the delivery.
This optional assignment is also possible in an inventory transfer request or an A/R reserve invoice.
Once you have allocated the serial number in the sales order, the serial information will be copied to target documents for picking, delivery or invoicing
After the serial number is assigned to a sales order, you cannot select it for another document, without canceling the serial number allocation in the original document. Closing or canceling the sales order automatically cancels its serial number allocation.
When you copy the sales order to a target document, such as a delivery, the Serial Number window will open automatically so that you can confirm that this is the serial number you wish to use or you can update it with a new serial number.
However, once the serialized item leaves the warehouse on a delivery document, you can no longer view or change the serial numbers on an A/R invoice. If a credit memo is created, then you will be able to view the serial number window to confirm or update serial numbers.
IV/ Summary
Here are some key points:
- Serial numbers track each individual unit of an item.
- Batches track a quantity of an item with characteristics in common.
- You have the option to set the serial numbers or batch numbers to be assigned on every transaction or to be assigned on release only.
- The management method “on every transaction” mandates that you assign serial number attributes for every single unit at the first point it enters inventory.
- “On release only” means that serial numbers are only required on documents that issue an item out of a warehouse.
- You can optionally assign serial and batch information on sales orders, inventory transfer requests and A/R reserve invoices.